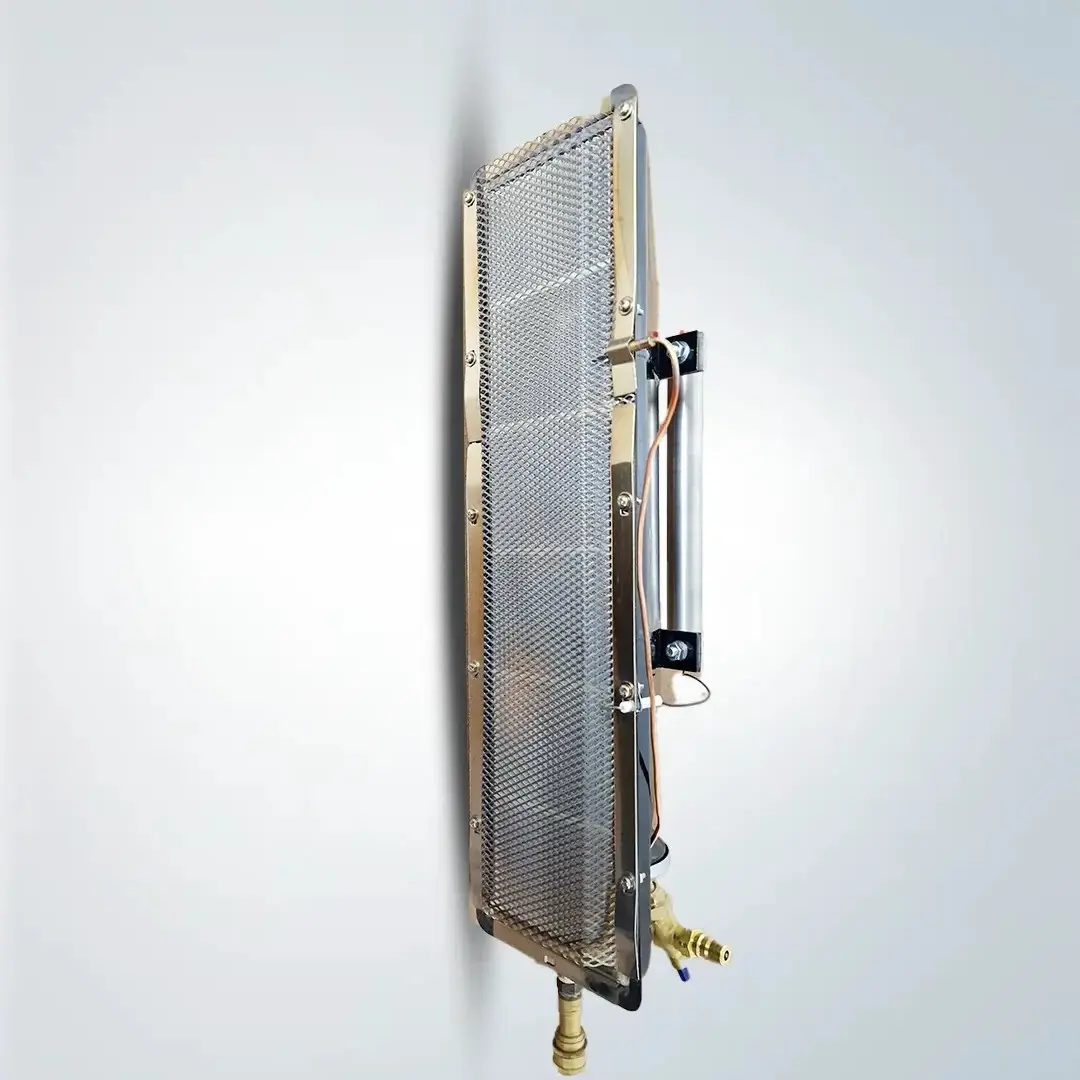
DESCRIPTION
Hot face bottled or piped propane or natural gas enters the rear of the burner by means of a self-sealing, quick release coupling. Combustion air is entrained by gas as it passes through the injector. A deflector in the burner case spreads out the mixture over the full hot face which is made up of rectangular ceramic plaques, each containing hundreds of tiny holes.
As the gas/air mixture emerges on the front plate of the plaques, it is ignited with an electric spark and continues to burn on the plaque surface. The plaques become intensely hot therefore being made from a modern ceramic material will withstand 1000°C (1800°F) on the hot face and yet run cold on the back face where the gas/air mixture enters. A domed, expanded Inconel mesh grill which protects the plaques from mechanical damage also helps to retain combustion loss to the hot face.
When positioned 50mm-75mm (2”-3”) away from the work piece to be heated, 50 000 BTU’s (for 600mm x 150mm) of energy will be directed at its surface. Heat transfer is mainly by radiation and the 1000°C (1800°F) radiating surface of the burner permits rapid heating to be achieved.
To facilitate quick burner attachment, a range of Cooperheat stands and magnetic feet can be supplied as optional extras.